
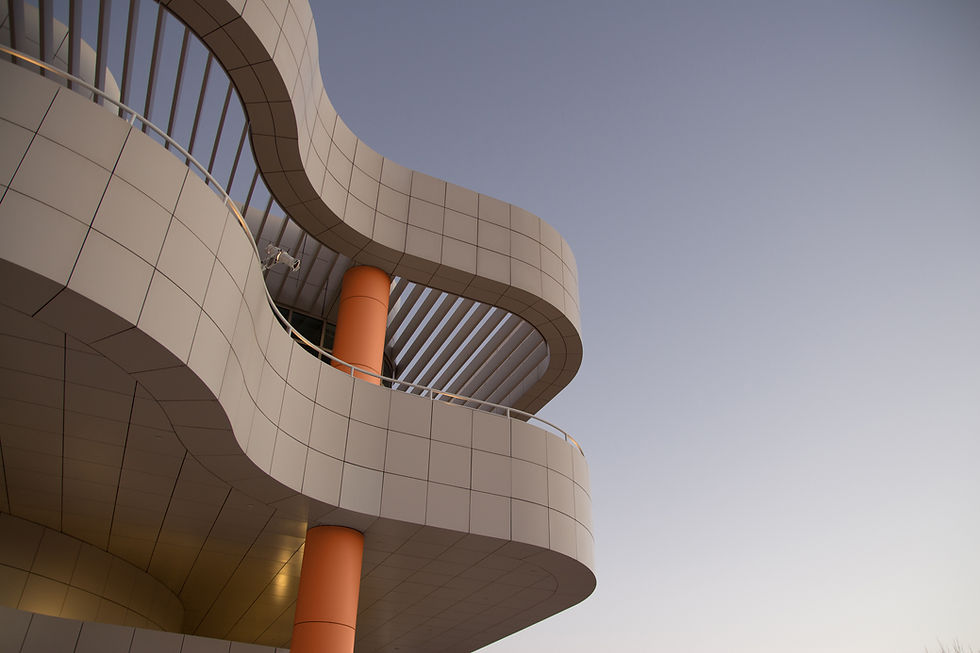

Ultrahigh Vacuum Systems: An Overview of Turbomolecular Pumps, Diffusion Pumps, and Gauges
Ultrahigh vacuum systems play a crucial role in various scientific and industrial applications where a clean and controlled environment is essential. Turbomolecular pumps, diffusion pumps, and gauges are key components of these systems, each serving a specific purpose in maintaining ultra-clean and low-pressure conditions.
Turbomolecular pumps are known for their high pumping speeds and efficiency in removing gas molecules from the vacuum chamber. These pumps operate by utilizing rapidly spinning blades to propel gas molecules towards the exhaust, creating a high vacuum environment. They are commonly used in applications where a high level of cleanliness and low-pressure environment is required, such as in semiconductor manufacturing and surface science research.
On the other hand, diffusion pumps operate on a different principle by using a heated oil vapor to capture and remove gas molecules from the vacuum chamber. These pumps are particularly effective in achieving very low pressures and are often used in conjunction with turbomolecular pumps to create ultrahigh vacuum conditions. Diffusion pumps are commonly found in applications such as mass spectrometry, electron microscopy, and thin film deposition.
In addition to pumps, gauges are essential instruments used to monitor and control the pressure within the vacuum system. Various types of gauges, such as ionization gauges, Pirani gauges, and capacitance manometers, are employed to accurately measure the pressure levels in the vacuum chamber. These gauges provide valuable feedback to ensure the system is operating within the desired pressure range and help maintain the integrity of the ultrahigh vacuum environment.
In conclusion, ultrahigh vacuum systems rely on a combination of turbomolecular pumps, diffusion pumps, and gauges to create and maintain clean, low-pressure environments for a wide range of applications. Understanding the function and importance of these components is essential for achieving optimal performance and reliability in ultrahigh vacuum systems.
Introduction to Ultrahigh Vacuum Systems
Ultrahigh vacuum systems are crucial for contamination-free environments in scientific and industrial applications, maintaining pressure levels of 10^-9 to 10^-12 mbar. They use special materials, surface treatments, and pumping techniques like turbomolecular, ion, cryogenic, and getter pumps. These systems involve components such as vacuum chambers, pumps, gauges, valves, and feedthroughs made of materials like stainless steel, aluminum, or titanium to achieve ultra-clean conditions for research and industrial processes.
Understanding Vacuum and its Applications
Vacuum, in the context of physics and engineering, refers to a space devoid of matter, particularly air. It is a state where the pressure is significantly lower than atmospheric pressure. Understanding vacuum and its applications is crucial in various fields such as manufacturing, research, and technology.
In manufacturing, vacuum plays a vital role in processes like vacuum forming, where a heated sheet of material is shaped over a mold by applying vacuum pressure. This technique is commonly used in industries to create products with intricate shapes and details. Additionally, vacuum impregnation is another manufacturing process where air and moisture are removed from porous materials by subjecting them to a vacuum, followed by the introduction of a liquid to fill the voids.
In research, vacuum chambers are utilized to create controlled environments for conducting experiments. These chambers allow scientists to study the behavior of materials under low-pressure conditions, simulate outer space environments, or investigate the properties of gases at different pressures. Understanding how vacuum affects various materials and substances is essential for advancing scientific knowledge and developing new technologies.
Furthermore, vacuum technology is widely applied in everyday devices such as vacuum cleaners, refrigerators, and fluorescent lighting. These devices rely on the principles of creating a vacuum to operate efficiently and effectively. For example, vacuum pumps are used to remove air and create a vacuum in refrigeration systems, allowing for the efficient cooling of food and other perishable items.
A comprehensive understanding of vacuum and its applications is fundamental in numerous fields, from manufacturing to research and technology. By exploring the properties and uses of vacuum, scientists and engineers can continue to innovate and develop new solutions that benefit society and drive progress in various industries.
Ceratek has over 20 years of experience with building custom UHV vacuum systems, from PLD chambers to Sputter coating systems, we have the experience you need for custom vacuum based systems.
Importance of Ultrahigh Vacuum in Research and Industry.
Ultrahigh vacuum plays a crucial role in both research and industry due to its ability to create an environment with extremely low pressure and minimal presence of contaminants. In research, ultrahigh vacuum conditions are essential for studying surface processes, thin film growth, and material interactions at the atomic and molecular levels. This controlled environment allows scientists to investigate fundamental properties of materials, explore surface chemistry, and develop new technologies with high precision and accuracy.
Moreover, in the industrial sector, ultrahigh vacuum technology is utilized in various applications such as semiconductor manufacturing, thin film deposition, and nanotechnology. The cleanliness and stability provided by ultrahigh vacuum systems are vital for ensuring the quality and reliability of products in industries like electronics, optics, and materials science. By operating in ultrahigh vacuum conditions, manufacturers can achieve superior product performance, reduce contamination risks, and enhance production efficiency.
The precise control and purity offered by ultrahigh vacuum environments enable researchers and industry professionals to push the boundaries of what is possible, leading to groundbreaking discoveries and technological advancements.
Turbomolecular Pumps: Key Components and Functionality
Design and Operation of Turbomolecular Pump based systems
Turbomolecular pumps are sophisticated devices used in various high-vacuum applications due to their ability to achieve extremely low pressures. These pumps operate based on the principle of momentum transfer, where rotating blades accelerate gas molecules towards the exhaust, creating a vacuum. The design and operation of turbomolecular pump-based systems are crucial for their efficiency and performance.
In terms of design, turbomolecular pumps consist of multiple stages of rotating and stationary blades arranged in a specific configuration to maximize gas molecule acceleration and minimize backflow. The materials used in the construction of these pumps are carefully selected to ensure compatibility with the gases being pumped and to withstand the harsh operating conditions.
The operation of turbomolecular pump-based systems involves careful control of parameters such as rotational speed, gas flow rate, and inlet pressure to optimize performance. Additionally, proper maintenance and monitoring of these systems are essential to prevent issues such as blade wear, contamination, or overheating, which can affect pump performance.
Applications and Advantages of Turbomolecular Pumps
Turbomolecular pumps are essential devices in various industries and scientific fields due to their exceptional performance and efficiency in creating high vacuum conditions. These pumps are widely used in applications such as semiconductor manufacturing, research laboratories, mass spectrometry, and surface analysis.
One of the key advantages of turbomolecular pumps is their ability to achieve ultra-high vacuum levels, which is crucial for processes requiring a clean and controlled environment. By efficiently removing gas molecules from a chamber, these pumps enable precise and reliable measurements in analytical instruments and ensure the quality and purity of materials in manufacturing processes.
Moreover, turbomolecular pumps are known for their compact size, low vibration, and minimal maintenance requirements, making them ideal for integration into complex systems and equipment. Their robust design and long operational life contribute to cost savings and uninterrupted operation in critical applications.
In addition to their technical advantages, turbomolecular pumps offer environmental benefits by reducing the consumption of resources and energy compared to other vacuum technologies. This sustainability aspect is becoming increasingly important in modern industries, driving the adoption of turbomolecular pumps as a reliable and eco-friendly solution for creating and maintaining vacuum environments.
Diffusion Pumps: Operating Principles and Performance
Diffusion pumps are a type of vacuum pump that operates based on the principle of high-speed jet action to create a vacuum. The performance of diffusion pumps is crucial in various industries where a high vacuum level is required, such as in semiconductor manufacturing, space simulation chambers, and research laboratories.
The operating principle of a diffusion pump involves the use of a high-speed jet of vapor to direct gas molecules towards the pump outlet. This creates a continuous flow of gas molecules through the pump, effectively reducing the pressure within the system. The vapor jet is typically generated by heating a special fluid, such as silicone oil or mercury, which then evaporates and forms a vapor stream that entrains gas molecules and carries them towards the exhaust.
One key aspect of diffusion pump performance is its pumping speed, which is a measure of how quickly the pump can remove gas molecules from the system. Pumping speed is influenced by factors such as the design of the pump, the temperature of the pump fluid, and the size of the pump inlet. Additionally, the ultimate pressure that can be achieved by a diffusion pump is determined by the pump's ability to effectively remove gas molecules from the system.
In order to maintain optimal performance, diffusion pumps require regular maintenance and monitoring. This includes monitoring the temperature of the pump fluid, checking for leaks in the system, and ensuring that the pump is clean and free of contaminants. Proper maintenance is essential for ensuring the longevity and efficiency of diffusion pumps in various applications where a high vacuum level is essential for operation.
The Role of Gauges in Monitoring Ultrahigh Vacuum Systems
In the realm of ultrahigh vacuum systems, gauges play a pivotal role in ensuring the efficiency and reliability of the setup. These gauges are essential instruments that provide crucial data about the pressure levels within the vacuum chamber. By monitoring and measuring these pressure levels, gauges help in maintaining the desired vacuum conditions required for various processes such as thin film deposition, surface analysis, and particle accelerators.
There are several types of gauges used in ultrahigh vacuum systems, each serving a specific purpose and operating within different pressure ranges. For instance, ionization gauges are commonly employed for measuring extremely low pressures, while capacitance manometers are preferred for higher pressure ranges. The data collected from these gauges not only allows operators to ensure the vacuum system is functioning within the desired parameters but also helps in detecting any leaks or irregularities that could compromise the vacuum integrity.
Furthermore, the integration of advanced technologies such as digital displays and remote monitoring capabilities has enhanced the efficiency and convenience of using gauges in ultrahigh vacuum systems. Real-time data acquisition and analysis enable operators to make informed decisions promptly, leading to improved process control and productivity.
Gauges are indispensable tools in monitoring ultrahigh vacuum systems, providing valuable insights into the pressure conditions within the chamber and facilitating the smooth operation of various scientific and industrial processes that rely on vacuum technology.
Various Types of Vacuum Gauges and Their Operational Principles
Pirani Gauges: These gauges are utilized for gauging the pressure of gases or liquids within a system. They commonly comprise a Bourdon tube that distorts under pressure, leading to the movement of a needle across a scale.
Cold Cathode Gauges: These gauges are employed to measure the temperature of a system or environment by utilizing mechanisms like bimetallic strips or thermocouples to identify temperature variations and exhibit them on a scale.
Mass Flow Gauges and Mass Flow Controllers: These gauges determine the fluid flow rate in a system, usually by employing a turbine or paddle wheel to calculate the flow rate.
Ion Vacuum Gauges: These gauges gauge pressure below atmospheric pressure, particularly in vacuum and ultrahigh vacuum systems. Ion gauges are best used between 10^-4 torr to 10^-12 torr
Significance of Gauge Readings in Vacuum Control
Gauge readings play a crucial role in vacuum control systems as they provide essential information about the pressure levels within a vacuum chamber. These readings are significant because they allow operators to monitor and adjust the vacuum conditions to ensure optimal performance and efficiency of the system.
By interpreting gauge readings, operators can determine if the vacuum pressure is within the desired range for the specific application. This information is vital for maintaining the quality and integrity of processes such as thin film deposition, semiconductor manufacturing, and vacuum distillation, where precise pressure control is essential for achieving desired outcomes.
Moreover, gauge readings help in identifying any potential leaks or malfunctions in the vacuum system. Sudden fluctuations or abnormal readings can indicate issues that need to be addressed promptly to prevent downtime and maintain the overall functionality of the system.
In addition, gauge readings are also crucial for ensuring the safety of the equipment and personnel working with vacuum systems. Monitoring pressure levels accurately can help prevent overpressure situations that could lead to equipment failure or other hazardous conditions.
Ceratek has over 20 years experience in developing custom ultrahigh vacuum systems including:
DC & RF magnetron sputter coating systems
Chemical Vapor Deposition (CVD)
Plasma Enhanced CVD systems
RIE and DRIE etching systems
Ar/O2 plasma etchers and ashers
Pulsed Laser Deposition (Excimer, YAG, OD/ID tube coating)
Thermal Evaporator Systems (Graphite, Tungsten, Laser, and Induction heated)
Vacuum furnaces and custom vacuum ovens
Modified CVD lathes for fiber optic preforms
Mass Flow controllers and gas switching systems